A Peavy Truss Rod Repair
This Peavy T-40 bass is unplayable because the neck has a crazy forward bow and the truss rod isn't able to coax it straight again. To make matters worse, the neck has separated at the glue seam and is distorted to the point that it appears the truss rod is being pulled up through the neck. The adjustment nut is only accessible with a deep socket because the rod has been pulled so far forward.
Peavy used Fender's design of a micro-tilt neck angle adjustment which pushes against an aluminum disc inlaid in the heel of the neck. I figured that would be perfect for hiding an exploratory hole as I couldn't see anything from the factory square hole. The disc popped out pretty easily and I drilled out until I could see the truss rod before switching to a chisel. Now the issue is apparent.

Peavy built their necks from two pieces of maple glued together and routed one half of the truss rod channel into each board. They would've placed the truss rod into one of the neck halves before gluing them together. This differs from Fender's methods of using a separate piece of maple for the fingerboard or routing a 'skunk stripe' into the back of the neck to facilitate installation.
This style of truss rod is a steel rod, laid in a curved channel, anchored at one end and threaded at the other with an adjustment nut that bears against the surrounding wood. As you tighten the nut, it pulls on the rod which forces the wooden neck to bend against the force of the string tension. If the anchor isn't stationary or if the wood behind the adjust nut is too soft, you can't get enough tension on the rod to bow the neck and the truss rod will not work.
I haven't torn into a functional Peavy neck to see what it's supposed to look like but I'd bet the truss rod anchor is supposed to be about 3/4" away from where it's currently located. They must not have left enough maple in the truss rod recess to support the nut and it began compressing and pulling through the maple.
I've seen a few other Peavy instruments online with splits in the neck which would lead me to believe this isn't a rare issue.
 |
Truss rod anchor (and spoiler of what is to come) |
The truss rod is a 3/16" diameter steel rod with a formed head at the end. I figure they ordered exceptionally long #10-32 bolts. The head or anchor of the truss rod is only 3/8" square and is rounded over from the manufacturing process which doesn't bode well for something you want to remain stationary.
The First Fix
I loosened the truss rod nut and used a small hammer to tap the truss rod as far back as it would go with the nut still attached. I used a maple dowel and a water-proof sharpie (which is lacquer-based) to mark contact points on the dowel that I would remove with a small round rasp. I repeated this until the dowel touched the bottom of the hole and then I copied that shape into a Bolivian rosewood (pau ferro) dowel. I used a chisel to cut a square recess in the doewl to capture the anchor and then I glued it into place with a 9-1/2" radius block on the fingerboard to force the bulging wood back down.
After letting the glue dry, I started tightening the truss rod and was able to pull the neck into a back bow but, unfortunately, it pulled the neck apart again and ruined my repair.
The Second Fix
After that failure, I wanted to start over fresh because it was clear that this anchor wasn't going to stay in place.
I whipped up a routing template and attached it via the neck mounting screw holes, I routed down until I clipped the truss rod anchor (with a cheap bit). I used a chisel to excavate around the steel rod and remove the remaining pau ferro before switching to a Dremel to lop the truss rod off at the anchor. My cut off wheel was too large so I ran it on the floor of my shop to reduce the diameter. I also kept a small squirt bottle of water to cool the steel.
With the truss rod no longer captured in place, I tightened the truss rod nut to pull the rod forward until I was able to grab the rod with pliers and pull. It came out fairly easy, there wasn't a lot of glue residue in the channel.
With the truss rod removed, I was able to switch to a nicer, bearing router bit and get back down to clean maple. I chose to rout a little deeper into the neck than the original channel so I could press the bulging fingerboard back down. It also helped me remove any of the compressed fibers.
Fabricating a Truss Rod
Truss rods need to be made from a high-carbon steel and it isn't something that you local hardware store is going to carry, in my experience. We're not building bridges but you don't want the rod to snap or your threads to shear because the only thing worse than replacing a truss rod is having to replace a truss rod a second time.
In the process of learning this, I did put some junk truss rods into cheap guitars and found out for myself. All-thread is a poor choice because threads weaken a steel rod and an entire rod of threads is about as weak as you can get. They are prone to stretching which would make a truss rod ineffective. Mild steel rods are common in home improvement and hardware stores and are sold as 'weldable steel', 'hot rolled', or 'cold rolled' but are too soft to hold threads for what we are doing. I put a mild steel truss rod in an Egmond plywood acoustic and stripped the threads off before getting anywhere close to straightening the neck, bleh. Don't bother.
I use O1 tool steel for making truss rods because it's available in a bunch of sizes and is known for keeping strong threads while being workable with hand tools. I've read that machinists also prefer 12L14 for threading because the lead in the alloy makes it a bit softer and easier to work. What you want is commonly sold as 'drill rod' and you want it to be annealed. I called a couple places locally before going online and ordering some 36" long rods.
For the anchor and nut, I like to follow the precedent set by the big manufacturers because they had it figured out decades ago. The truss rod material should be just as strong as the anchor material (if you are threading) and should be far stronger than the adjustment nut. Gibson uses brass for their adjustment nuts and Fender uses aluminum for their traditional, heel-adjust models. If you are absolutely torquing the nut, you want the threads in the nut to fail before the threads on the rod because one is far easier to replace.
Threading
Threading isn't as bad as it seems if you have quality tools. I suffered with a dirt cheap tap and die set before throwing it out and just buying taps and dies as I needed them. It's $10 at my local hardware store for a 10-32 tap and die and I already had a die stock and tap handle to use them.
I have brass jaws on my bench vise so I popped the drill rod into the vise, horizontally, with about half an inch protruding from the side. Brass won't mar the steel so I can tighten the jaws down. Using a flat file, I flattened the end of the rod and then beveled it at something near a 45 degree angle to help the die start on center. Using one hand to apply pressure onto the rod, I used the other to slowly turn the die until I felt it bite into the rod. I stand to the side of the rod so I can watch my die stock as I turn it and ensure it's, visually, at the same distance from the vise throughout the entire rotation. That helps me determine if I'm cutting straight down the rod or at an angle. A little 3-in-1 oil helps lubricate the cutting action and I back off a quarter turn frequently to break the chips.
I cut about 1-1/4" worth of threads on the rod, same amount as I found on the original truss rod, before holding it up to the neck of the guitar, marking where I wanted it to end, and cutting to length with a hacksaw. I filed that end square before repeating my beveling step, popping it in the vise, and tapping 3/16" worth of threads on that end.
I had a piece of 1/8" thick, annealed O1 tool steel that I bought to make plane blades which will be perfect for my anchor. I spray painted one side of the bar and let it dry in the sun before using a square and a cheap carbide scribe to layout my rectangle anchor. I scribed lines to connect the corners to find the center and hit it with a punch. Before cutting the anchor out of the bar, I checked a tapping chart to determine the right size of drill bit for #10-32. I predrilled with a bit about half the size of what I would finish with and used a rotary burr in my drill to lightly deburr the hole. Then I used a little oil and a tap wrench to cut the threads into my stock. Lastly, using my Dremel, I cut the steel bar to my scribed lines and popped it in the vise to clean up the edge surfaces.
The truss rod is not centered inside this neck and actually the two halves of the neck aren't centered either. The anchor is slightly longer on one side than the other but there is plenty of material on the smallest side so I'm not concerned. Turning the neck around, I grabbed two Gibson-style truss rod nuts (same thread) and ran them up the rod before tightening one against the other to create a jam nut. Now I could turn the rod and thread it into the anchor.
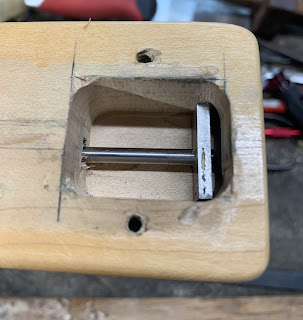
Testing
Before gluing or setting anything permanently, I wanted to confirm that this was a success so I needed to plug the rest of the hole that I routed out earlier. I have some maple, approximately 1" by 2", that I got from the hardware store because it had a little bit of 'birdseye' figuring and it happens to be ridiculously hard. It doesn't dent under my fingernail and on the belt sander, it abrades slowly and the end grain is very quick to scorch. I marked two 1/2" diameter circles on the board and cut my plugs to fit the holes.
I flipped the neck over and began tightening the truss rod and was thrilled when the neck was able to be pulled into a considerable back bow without any movement of the fretboard crack.
Assembly
Disassembling the truss rod was slightly less fun as I had to loosen the adjustment nut, tap the rod backwards, and pull the maple blocks out before using vise grips to unscrew the rod from the anchor and removed both from the neck.
Nobody wants a truss rod that rattles inside the neck, and since I broke the glue residue in the channel when I pulled the original rod out, I wanted to make sure that I was covered. Silicone is a common choice but it was too viscous to flow down into the channel so I used clear, non-expanding polyurethane glue because it remains flexible after curing and introduces no water into the neck. I coated the truss rod in paste wax before reinstalling it through the headstock to prevent any sticknig.
As the truss rod end came into view, I cleaned the threads off with a solvent and a shop towel before applying Loctite Threadlocker 271 to the rod and the anchor. The truss rod will snug itself up when you tighten it and can't move any further but I wanted to prevent the rod from backing out as you loosened the truss rod. 271 is considered permanent unless you heat it up to 500 degrees Fahrenheit.
I coat the maple blocks with Titebond before tightening the truss rod to lock everything in place. A fillet of maple is glued in between the blocks to cover the rod and provide a surface for the aluminum micro-tilt disc to be inlaid back into the neck.
Final Thoughts
 |
The truss rod tightened down |
I believe the failure of this truss rod to be from a manufacturing defect that didn't leave enough maple for the anchor end to rest against and that caused it to pull through the neck. This was worsened by the small size of the anchor and the rounded face which made it easier for the wood to crush and be pushed out of the way. Lastly, the design of the truss rod includes a dip down, past the end of the channel's curve, to fit the anchor and that meant that the anchor was being pulled up towards the fingerboard instead of in line with the neck.
My anchor is positioned so that it pulls straight toward the headstock and intentionally made large enough to spread the force against as much maple as possible.
 |
A crude illustration of the neck's cross section The original design is on top, my new truss rod is on bottom |
Visually, the repair could've been better if I had jumped straight to cutting the truss rod out rather than trying to glue the crack, testing a truss rod repair, and having the crack reopen along. Light colored woods are super tough, you really only have one attempt to make it invisible without breaking out your artist's palette. If this was a rosewood board, I'd sand it and use CA to bind a patch of rosewood dust to the crack and it'd be an invisible repair.
Did it work?
Yes.... No.
With the new truss rod, I was able to put the neck into a considerable back-bow without cracking or separating the neck which is a massive improvement from where we started. That was a successful truss rod replacement and should've guaranteed success. Minutes after tuning the bass up to pitch, the neck began pulling forward and ended up exactly where we started, damn... I tightened the truss rod, to no avail, and eventually felt it start crushing the wood fibers at the headstock end - failure.
Would a heat press save the neck? eh. The speed in which the bass went from an 1/16" of back bow to a 1/16" of forward bow has me suspecting this piece of maple was destined to fire off arrows rather than riffs.
An experimental repair would be to rout slots in the back of the neck, not unlike a Fender skunk-stripe, inlay carbon fiber strips, and cap with wood before carving to match the neck profile. That's a couple days worth of work for a $600 bass and no guarantee of success. I'm calling it quits. Hopefully if you find yourself in the same scenario, this might help you work through a truss rod replacement and hopefully you have better luck than I did. Not all pieces of hard maple are created equal.
Related Reading
I enjoy reading blogs about complicated or unusual guitar repairs and I've referred to these in the past when I've replaced truss rods.
Strange Guitarworks on fixing a Gibson Grabber bass with a broken truss rod and broken scarf joint.
Strange Guitarworks, again, on replacing a Fender Jazz Bass truss rod by removing the skunk stripe.
Jack's Instrument Services replacing a truss rod on a Fender Music Master with a hair-raising move to cut into the fingerboard to reach the anchor.
Haze Guitars on a Gibson ES-335 with a truss rod channel cut too deep into the neck - unfortunately I couldn't find a follow up to this post.
Strange Guitarworks, I like their content, on replacing a truss rod in an Epiphone Rivioli by removing the last couple fret's worth of fingerboard to access the anchor.
Follow Us
I'm a college student who is fascinated with guitars and collecting and repairing them